Our service
Injection molding
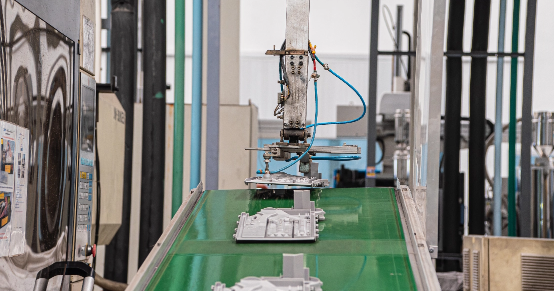
This involves the process of using heated plastic material that is then injected into a pre-formed mold to create a product in its desired shape. Different materials can be used including thermoplastics, thermosets, or elastomers. Secondary processing such as painting, coating, and assembly may also be required.
Secondary processing
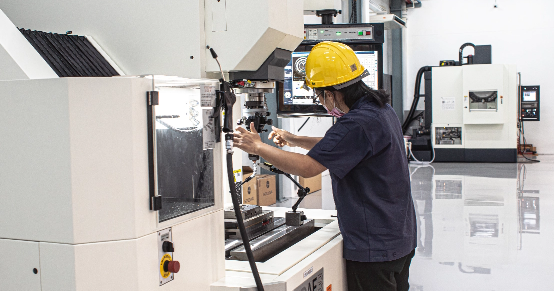
This involves the application of additional treatments to a product after it has been molded to produce a finished product. This could include painting, coating, or assembly. This can improve the aesthetics or functionality of the product.
Tool & die manufacturing
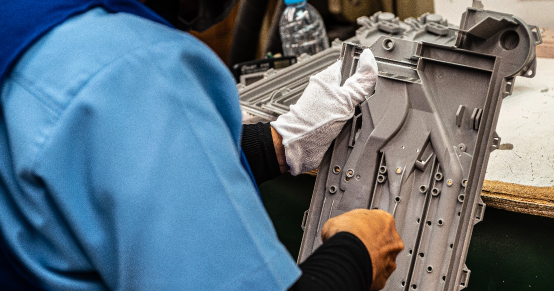
This involves the production of molds and dies used in the injection molding process. The tools and dies must be designed to the exact specifications of the desired product, taking into account the size, shape, and functionality of the product. The tools must be able to withstand extreme temperatures and pressure, and must be accurately machined and polished for high-precision results.
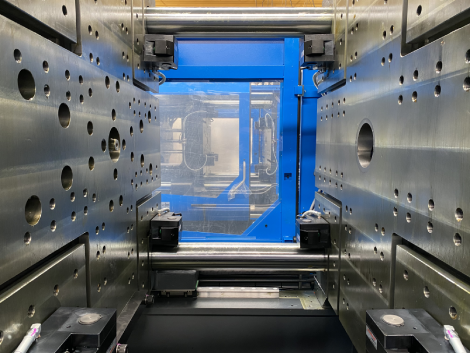
Precision Injection Molding
40+ years of precise thermoplastic injection moulding application in 3C, household appliances and automotive industries with a vast variety of materials with single / double color injection.
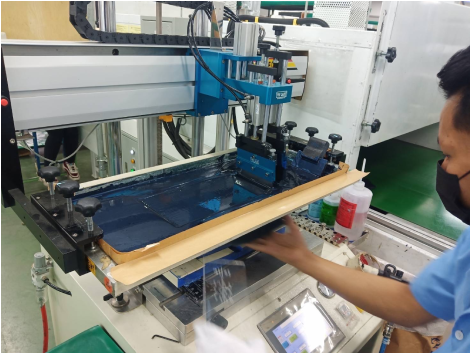
Secondary Processing
Part secondary processes include: spray painting, silk screening, pad printing, ultrasonic welding, hot stamping, laser marking, sub assembly.
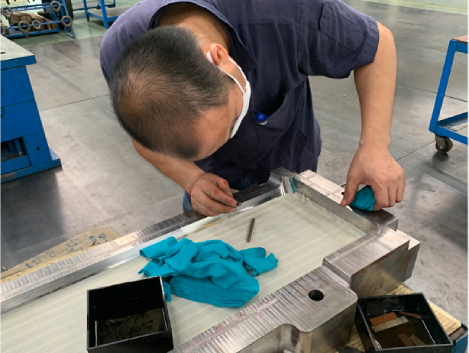
Tool Fabrication
In-house tooling able to fabricate tools for machine range from 40 - 1600 tonnes. With high precision CNC / Sinker EDM / wEDM, helps to satisfy the needs within various industry fields.
Injection molding
We are committed to produce high precision thermoplastic injection parts with best in class practices while delivering our solution to our customer in a timely manner. Our team is proactive in managing from material lead-time, delivery lead-time and any issue that may occur, thereby providing great feedback and collaboration with our esteem customers. The services range from single to double color injection molding processes, as well as gas-assist process and insert molding. The machine service ranges from 50T - 1600T machines, with each production cell unit accompanied by the required accessories that could fulfil mold and production requirements. Our injection presses are best in class meanwhile with precision gas assist and equipment from Bauer Kompressoren, we are able to generate nitrogen at precise nitrogen % levels, delivering consistent gas requirements for molding purposes.
Secondary processing
Post processing of injection molded parts are available and we are open to increase and improving our capabilities as our customer’s requirements changes. At JET we are always looking to expand beyond and incorporate new and innovative approaches.
Available processes
Spray painting process
To color and apply toned finishes to the surface of items, commonly used on appearance items . These processes are done with automated robots that is efficient in detailing the same quality and spray quantity for every single part.
Silk Screen printing process
Available to print desirable texts or logos on to the surface of plastic injection-molded products
Ultrasonic welding process
For plastic components that could not be injected as such, the process welds parts into a single piece of item through the Ultrasonic process.
Hot stamping process
Available to fabricate metallic or other surface finishes as requested.
Laser marking process
Service includes logo marking, product appearance alteration, paint removal and other text additions to the product surfaces.
Sub assembly lines
includes assembly processes such as sticker pasting, product assembly, heat melt process and other upon requested.
Spray painting process
To enhance product apperances through spray painting with auomated robots for precise and consistent appearnace finishes.
Silk Screen / Pad printing process
Silk screening or pad printing for your cosmetic apperances. From Logo, branding to functional indicators, we are able to assist.
Ultrasonic welding process
Combining plastic molded parts into a single functional product, this allows shapes that are otherwise impossible.
Hot stamping process
For Metallic finishes as part of the cosmetic apperanace enhancement on your thermoplastic products.
Laser marking process
Allowing transparency, or functional markings on the plastic products produced.
Sub assembly lines
Various sub assembly on the molded parts are available, these includes welding, heat melt and assembly of non plastic parts.
Tool and die manufacturing and maintenance
JET’s tool manufacturing capabilities are assisted with on-site high precision machining centers such as CNC, EDM, Wire-cut as well as other assisting machines in the likes of laser welding, drilling and grinding.
Range of Tool Tonnages start from 50T to 1600T and customer 3D and 2D drawings could be analysed, with the tool being designed, manufactured and trialed on- site. Hence creating efficiency for your production lead- time.
Maintenance procedures are also part of the agenda which includes cavity surface cleaning, cooling channel, product issue fixes and texture maintenance.
Range of Tool Tonnages start from 50T to 1600T and customer 3D and 2D drawings could be analysed, with the tool being designed, manufactured and trialed on- site. Hence creating efficiency for your production lead- time.
Maintenance procedures are also part of the agenda which includes cavity surface cleaning, cooling channel, product issue fixes and texture maintenance.
Our services process
1. Product onboarding
During the new product initiation phase we are able to discuss and analyze prduction possibilities together with our customers. These may include tooling design or machine capability analysis depending on the specific services requested.
2. Trial and sampling
Trialing of suitable injection molding settings and conditions are core to the success and cost effectiveness of the specific parts produced. These are carefully designed, monitored and recorded for repeatability.
3. Mass production
On-time and adequate preparation to ensure our customer's production lines could be up and running uninterrupted. This is vital to JET in achieving value and cost effectiveness to our customers.
4. Quality assurance
Vast number of test and equipments are available to measure our own products and verify against cusomter's standards and requirements are met.
5. Delivery
Once the parts pass the quality assurance process, they are then packaged and shipped to the customer according to their requirements.
6. Mold maintenance
The final step in the injection molding process is mold maintenance. This involves regularly inspecting and maintaining the tooling and system to ensure that it continues to produce quality parts through cleaning, repairing, and replacing mold components as necessary.
We are able to provide assistance along each step of the way.
Lastest certificate